FEATURED: HYBRIT PROCESS – towards fossil-free steel
HYBRIT – short for Hydrogen Breakthrough Ironmaking Technology – is a joint venture between SSAB, LKAB and Vattenfall, aiming to replace coal with hydrogen in the steelmaking process. HYBRIT is a ground-breaking effort to reduce CO2 emissions and de-carbonise the steel industry.
As a demonstration of science and innovation, HYBRIT has the potential to sustain Europe’s leading position in fighting climate change while strengthening competitiveness.
Steel is one of the world’s most recycled materials.
Once it has been produced, the material can be used repeatedly via the scrap-based production route. Even though steelmaking from recycled scrap has been estimated to increase drastically, the overall demand for steel in the next few decades can only be met by utilising ore-based virgin iron as well.
The ore-based steelmaking value chain starts at the iron ore mine. After mining, the iron ore is processed, and a product rich in iron oxides is produced in the form of pellets, or fines. At the steelmaking plant, iron ore is converted to metallic iron by reduction of the iron ore pellets with coke in a blast furnace. The iron oxide and carbon then react to form CO and CO2 gases, as well as metallic iron. Now in liquid form, the iron is further processed before a semi-finished steel product is cast.
An alternative to the dominant blast furnace ironmaking route is to use the so-called direct reduction process where natural gas replaces coke as the main reductant, and the main product is solid sponge iron. The iron then needs to be melted using an electric arc furnace, before steel is produced.
Currently, this gas-based direct reduction process is not used in Sweden, but is an option in other parts of the world where natural gas is in abundance.
WATER INSTEAD OF CARBON DIOXIDE
The reduction reactions in ironmaking represent around 85 to 90 per cent of the total carbon dioxide emissions in the ore-based steelmaking value chain.
In addition, the energy-containing gas from coke ovens and blast furnaces has an important role as the main energy source for heating furnaces and materials. Fossil-free steel production will eliminate the formation of CO2, by using fossil-free reductants and energy sources.
In the case of HYBRIT, iron metal is produced by using hydrogen gas as the main reductant. The production route is similar to existing direct reduction processes, except for the carbon dioxide emissions: hydrogen reacts with iron oxides to form water instead of carbon dioxide.
H2 + FeO = Fe + H2O (Hydrogen + Iron ore pellets = Sponge iron + Water)
Hydrogen gas (H2) is produced by electrolysis of water using fossil-free electricity, which is already the standard in Sweden.
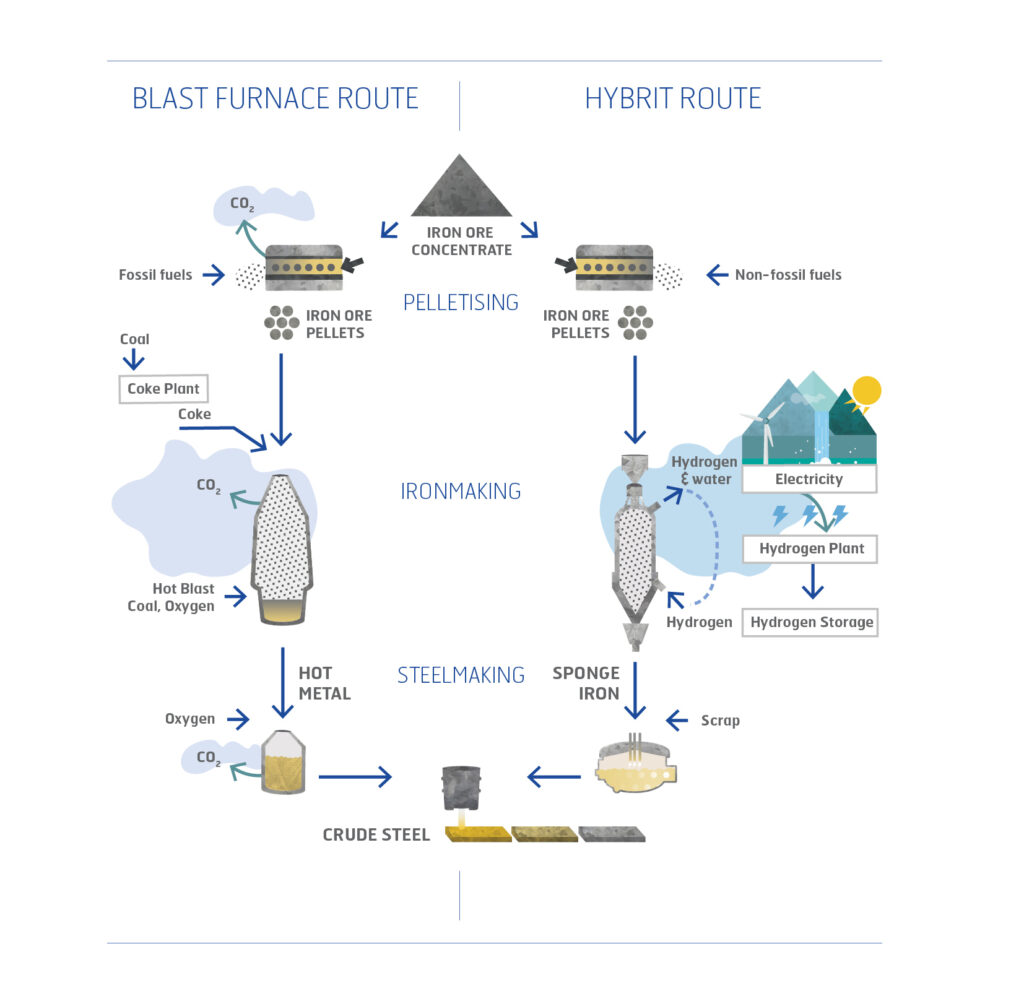
Figure 1. Comparison between the blast furnace-based steel production process (left) and the H-DR process to be implemented by HYBRIT (right).
PROMISING COSTS AND TECHNOLOGICAL POTENTIAL
The prefeasibility study results underline that no major, previously unknown technical obstacles have been identified. Nevertheless, considerable future development efforts will be required to realise and verify the concept, and to handle risks. These include fundamental research projects using models and laboratory scale experiments, as well as trials in pilot and demonstration plants.
Considering current cost levels, an iron- and steelmaking value chain based on the HYBRIT concept would result in a 20 to 30 per cent increase in the cost of producing crude steel. The cost structures of fossil and fossil-free value chains are strongly dependent on the prices of coking coal, electricity and emission rights. An expected future shift in costs and market demands makes the fossil-free HYBRIT concept an attractive alternative.
Large-scale hydrogen production and storage will allow for flexibility in power consumption on a large scale, which will favour the implementation of intermittent renewable energy sources for electricity production.
Large-scale hydrogen production will boost the transition to other hydrogen-based technologies and spur innovation and business spin-offs associated to the hydrogen society.
When calculating initial emissions of the current dominant production process, both direct and indirect emissions were included. In Sweden, the carbon dioxide emissions using current technology are 1.6–1.7 tonnes of CO2 per tonne of crude steel, compared to the estimated 2.0–2.1 tonnes of CO2 for a typical integrated steel plant in Western Europe.
The result can be explained by differences in the electricity mix, with more renewable sources available in Sweden. Another factor is the high level of energy efficiency in the Swedish industry, where LKAB and SSAB are leading operators in terms of energy and CO2 efficiency.
The estimated total cost per tonne of crude steel has been calculated based on current commodity and energy prices. The indication is that the production cost for steel via the HYBRIT route is approximately 20 to 30per cent higher than for the reference case. In the steel industry, commodity and energy prices may fluctuate considerably over time, and there are several factors indicating that the relative cost level can change during the HYBRIT planning horizon.
Although a complete replacement of carbon by renewable energy will result in an increase in material costs, the impact on the end-user product is negligible. Predictions of future costs are highly uncertain, but anticipated shifts in prices and market demands make the fossil-free HYBRIT concept a commercially attractive option.
CONVENTIONAL IRON/STEELMAKING
Even though the existing LKAB-SSAB production system is one of the most efficient of its kind worldwide, it emits around 6 million tonnes of carbon dioxide per year in Sweden.
IRON ORE
Typically, the fine iron ore concentrate contains more than 71 per cent iron.
PELLETISING
In the pelletising plant, the fine iron ore concentrate is dewatered, and a binding agent is added before the concentrate is rolled into 10-millimetre pellets. The pellets are dried, preheated, sintered, and cooled down before storage and transportation to steel plants.
The magnetite ores in northern Sweden are especially suitable for such processing. During the process, the magnetite is oxidised into hematite. This reaction releases heat, which replaces about two thirds of the fossil fuel needed when pellets are produced from hematite concentrate.
COKE PRODUCTION
Coke is a stable fuel and reducing agent with a high carbon content, made from coal. Parts of the volatile matter in coal are used as energy for the high temperature baking process in coke production.
BLAST FURNACE
The iron ore and coke is added to a process designed to release oxygen from the iron ore according to the simplified reaction:
iron ore + carbon => iron + carbon dioxide.
This takes place in a shaft furnace where the solids are charged to the top of the furnace, and preheated air is injected in the lower parts to enable an efficient heat transfer. The result is a molten hot metal consisting of iron, with 5% of dissolved carbon.
OXYGEN CONVERTER
The hot metal is refined with oxygen gas to lower the carbon content and form molten steel. The reaction releases heat, which is utilised to melt an additional 10-20% of steel scrap, before the liquid steel is tapped into a ladle, where the final chemical composition and the temperature of the steel is adjusted. After this, the steel is cast into crude steel slabs in a continuous caster.
CO2
Carbon dioxide originates from the blast furnace, coke making, decarburisation of hot metal in the converter process, and fossil fuels used in the pelletising process.
HYBRIT PROCESS IMPLEMENTED
The HYBRIT system uses hydrogen – produced using fossil-free electricity instead of fossil coal – and releases water instead of carbon dioxide. If realised on an industrial scale, the technology could make Sweden the world’s first country to produce fossil free ore-based steel.
PELLETISING
The fossil fuel in ore processing will be eliminated with an increased level of energy efficiency and by switching to fossil-free sources of energy.
HYDROGEN PLANT
Hydrogen production takes place by electrolysis of water into hydrogen gas and oxygen. Renewable electricity is the primary energy source. Electrolysis is a mature technology, and principally, there are no barriers to building a large-scale plant.
DIRECT REDUCTION
The existing direct reduction method needs to be adapted to reduction with hydrogen to eliminate carbon dioxide emissions. The off-gas of the reduction process would be water, according to the simplified reaction:
iron ore + hydrogen => iron + water
The result is a solid porous sponge iron, suitable for steelmaking.
ELECTRIC ARC FURNACE
The Electric Arc Furnace (EAF) is used for heating and melting charged materials by means of electric current. The use of EAFs allows steel to be made from up to 100% scrap metal, or as in the HYBRIT concept, from a mix of direct reduced iron and scrap. Similar to the conventional process, the liquid steel is tapped into a ladle where the final chemical composition and the temperature of the steel is adjusted, before it is cast into crude steel slabs in the continuous caster.
CO2
CO2 emissions will be reduced dramatically, although minor emissions can still arise because of the use of certain process equipment, and because small amounts of coal must be used in the manufacturing process.
TRANSITIONING TO HYBRIT TECHNOLOGY
Transitioning to HYBRIT is a two-decade venture that is still in its early stages. With full implementation to be complete by 2040, at the time of writing the project is just entering its pilot phase. This will be followed by a demonstration phase toward the latter half of the 2020s and a move towards full commercialization thereafter.
Metals processing, cement production and petrochemicals are all highly capital-intensive sectors whose products play key societal functions, while also currently having a massive footprint in terms of greenhouse gas emissions.
If these sectors are to transition to technological configurations that are compatible with global climate change mitigation ambitions, a host of innovations will have to be proven not just to be technologically viable but to function in a broader business and policy context as well.
Demonstration plants will be a central vehicle to this end.
THE CRUCIAL ROLE OF THE DEMONSTRATION PHASE
According to the original roadmap presented by HYBRIT, the plan is to have the first commercial facility in place in 2035. This is to be preceded by trials in a pilot plant (2018–2024) followed by a demonstration phase (2025-2035).
In addition to the H-DR plant, the pilot phase includes two additional components (HYBRIT 2019):
- Investigation and evaluation into using non-fossil energy (bio-oils and/or plasma technology) for heat in processing iron ore pellets. For this purpose, construction of a test facility in Malmberget began in April 2019.
- Construction of a test facility for hydrogen storage in Luleå, to be carried out in 2021. This facility will evaluate the use of lined rock cavern (LRC) technology for hydrogen storage and has more recently received complementary funding from the Swedish Energy Agency.
GROWING INTEREST IN H-DR STEEL: THREAT OR OPPORTUNITY?
Since HYBRIT was first presented in 2016 there has been a substantial increase in the rate of innovation in hydrogen-based iron reduction, with several European projects now operating in parallel with HYBRIT (Lechtenböhmer et al. 2018).
This represents a risk for HYBRIT, especially in the light of how, for example, SSAB has emphasized the strategic importance of being the first company to commercialize fossil-free steel.
A related issue that could become important is the expansion of the so-called “hydrogen economy” more broadly. The HYBRIT project could very well benefit from an expected growth of investment over the coming decade in hydrogen technology and infrastructure in the Nordic countries as well as globally.
These benefits could come both in the form of growing societal acceptance of hydrogen as an energy carrier, but also from reduced costs. In particular, the modular technology characteristics of electrolyzers indicate that mass-production could push their cost downwards, as has happened with both solar PV and Li-ion batteries.
The HYBRIT process is in several ways quite different from the incumbent blast furnace-basic oxygen furnace process in the steel industry. First, whereas the latter process is very mature and approaching its theoretical limits in terms of efficiency, parts of the HYBRIT process draw on relatively immature technologies that should hold potential for cost reductions.
This seems especially likely for the hydrogen production phase, because electrolyzers from a broad technology perspective are quite similar to solar PV and Li-ion batteries. They are modular and have economies of scale that are realized by adding more (largely identical) units rather than by only building bigger units.
This opens up prospects for mass-production, manufacturing automation and substantial cost reductions. In fact, with very low electricity prices and low capital costs for electrolyzers, the H-DR process has the potential to be cost-competitive with the blast furnace-basic oxygen furnace process even in the absence of a price on carbon.
In other words, while the policy landscape is noted as an important challenge in the pre-feasibility study, the H-DR process may in the long run turn out to be less vulnerable to policy fluctuations and CO2 price developments than CCS.
TWO HYPOTHETICAL DEMONSTRATION PLANTS: “SMALL” AND “LARGE”
A demonstration plant should be “sub-scale” and, in terms of capacity, lie somewhere in between a pilot plant and a commercial plant. However, this is still a quite broad range, as the H-DR pilot facility in the HYBRIT case has an iron ore reduction capacity that is a mere 1% of that of a commercial blast furnace.
Two hypothetical H-DR demonstration plants are distinctly different in terms of capacity. They are both significantly larger than the HYBRIT pilot plant yet significantly smaller than a typical commercial primary steel mill in terms of iron reduction capacity. The first one, called “small”, is a demonstration plant that is more akin to large pilot plant, whereas the second one, “large”, is closer to the size of a commercial facility.
The specifications for the two options draw on the assumption that the H-DR unit to be used for the HYBRIT demonstration phase will be based on existing DR shafts offered by MIDREX or Energiron.
“Small” is based on the smallest commercial DR system (an Energiron micro-module) and “large” was selected to be substantially larger than “small” but still with substantially smaller iron reduction capacity than corresponding blast furnaces on SSAB sites.
Table 2 gives an overview of the two hypothetical alternatives. Included for comparison are also specifications for the pilot plant and an envisioned future commercial facility. Note that the cost figures for the two hypothetical demonstration facilities should be seen as “guesstimates”.
Electrolysis capacities for the two demonstration plant alternatives and the commercial unit are based on estimations from MIDREX of 400 MW needed for a 1 million tons/annum H-DR shaft.
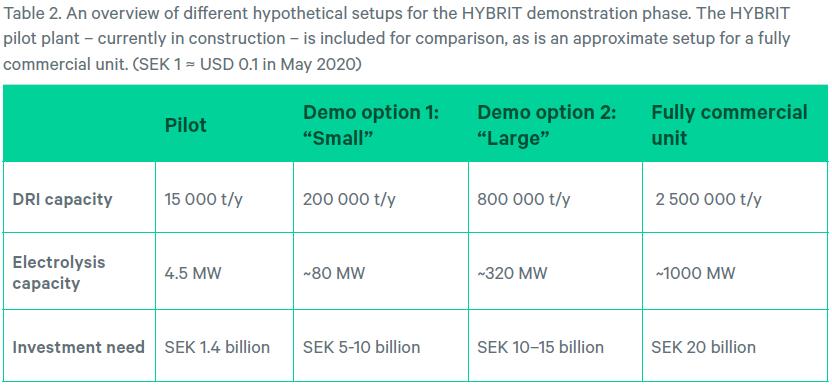
Source: Stockholm Environment Institute, SSAB, LKAB and Vattenfall