Steel rises to the challenges of Industry 4.0
The advent of more and more sophisticated artificial intelligence systems is allowing the steel industry to augment and improve its production processes
The steel industry is leading the way in ‘smart production’, and seizing the opportunities presented by the fourth industrial revolution.
From the steel industry’s perspective, Industry 4.0 means almost-autonomous steelworks. People, products and production facilities are fully connected through the Internet of Things (IoT).
Sensors collect vast amounts of data, and that information is then interpreted by artificial intelligence (AI). This optimises the production line and creates synergies across the facility.
Welcome to the smart factory.
THE BRAINS OF THE OPERATION
South Korean firm POSCO operates two of the largest steelworks in the world – in Gwangyang and Pohang – and produces 42 million tonnes of steel annually. Its POSFrame software platform amasses big data gathered by a huge cluster of sensors, and then sends it out to inform AI processes.
“Whereas before we had silos of data everywhere, now we put it all in there,” explains JinSoo Park, project leader for POSCO’s Smart Factory.
As the brains of the operation, POSFrame has had a lot to learn, and POSCO has been asking its most experienced staff to help educate its AI.
“Much of the great knowhow we have is hidden inside our operators or engineers. We’re trying to get that knowledge out of their heads and codify it into something that we can then call ‘intelligence’,” Park says.
“If you can’t measure it, you can’t manage it. If you can’t manage it, you can’t improve it.”
Peter Drucker
A quote from famed management consultant and author Peter Drucker is a guiding maxim for POSCO and other steel producers: “If you can’t measure it, you can’t manage it. If you can’t manage it, you can’t improve it.”
SAFETY, EFFICIENCY AND PRODUCTIVITY
Dr Franz Androsch, Head of R&D and Innovation at Austrian steelmaker voestalpine, stresses that this potential for the complete documentation of all production steps is what defines Industry 4.0 as a concept.
“A wide array of electronic measurement and monitoring systems automatically record, network, and use numerous machine and product parameters to control the machine and ensure quality. This makes it easier to plan downtimes, increase productivity, and ensure top quality.”
Know-how from the floor is at the heart of any smartsteelworks, and at the heart of any steelworks is the blast furnace.
voestalpine has already seen impressive results at its integrated facility in Linz. Blast furnaces need to be continually charged with alternating layers of coke and sinter; these layers ensure a uniformly efficient gas flow. Until recently topography and temperature irregularities were difficult to identify.
Now, using 3D-radar technology, voestalpine has been able to develop a comprehensive model of the charging process that includes real-time measurement of blast furnace conditions, which has led to higher yields and reduced emissions.
The convergence of experience from the factory floor and new technologies is also making for a safer place to work. Nippon Steel and Sumitomo Metal Corporation (NSSMC) are trying to predict hazardous situations before they occur in order to become a zero accident-workplace.
Engineers wear smart hardhats equipped with cameras, hazardous gas sensors and accelerometers. Geo-fencing technology provides an indoor positioning system within the plant. If a worker arrives in an area known to be dangerous the hardhat can alert them. Likewise, if they fall or end up in an abnormal position it alerts the system.
A DATA REVOLUTION
Data sets on the steelmaking process were available before, but the technologies of the fourth industrial revolution are unlocking new possibilities that allow steel producers to collect more data in different ways from of a myriad of smart sensors and smart systems that communicate over a local network.
For example, when a slab makes its way to the reheating furnace, laser sensors check the air intake. The results are fed back to the AI to get the right temperature on the plate. The heat of the top and bottom of the slab are then measured to gauge if there is a difference.
“It is so important to control that differential. Otherwise the slab will have to go through another rolling process,” POSCO’s Park says.
“The data allows us to trace back to exactly which operation and at which position a defect in a product occurs. On which shift and on which day, and under what conditions.”
JinSoo Park
“A slab can also get twisted in there, and that can wreak havoc on the production process and cause accidents.”
POSCO has been using time-based maintenance to keep its equipment in good working order, and smart factories open up greater possibilities for improving this.
“We’re trying to inject some kind of intelligence into our processes so we can do more predictive maintenance,” Park says. “That means we’re not only lowering the cost, but also reducing the unplanned downtime.”
Steel plants are 24/7 operations that have to be online. Just as you cannot replace an aeroplane’s engine while it is in the air, it is very difficult to replace individual units one at a time in the plant.
For Androsch, “digitalisation also changes how we interact with suppliers and customers, for example using new online platforms, apps, and other systems that offer order tracking and other services.” As such, it is opening up possibilities for entirely new business models.
Dr Martin Pei, Executive Vice President and Chief Technology Officer at Swedish steel producer SSAB foresees the development of an entire digital ‘manufacturing ecosystem’ in which the data accumulated by both downstream and upstream industries is incorporated through the whole value chain.
“Ecosystem participants get to provide new services and enter new business positions,” he says.
CONSERVING ENERGY
In addition to using data to make gains in productivity, steel producers are installing smart meters and other sensors to cut their CO2 emissions and reduce wasted energy.
Many plants generate a lot of their own electricity using the gas from their furnaces and rolling processes. However, many also use large amounts of power from the grid, which they are always looking to reduce.
Different steel grades need different amounts of energy and sensors are now able to measure exactly which grades of steel are the most energy intensive. Steel producers can then analyse energy pricing to position certain grades in the production line so that they are manufactured when power is cheapest.
MEASURE AND IMPROVE
AI is also cutting costs when products undergo hot-dip galvanisation. After the steel is dipped, a blade is positioned to cut it based on real-time measurements. This allows for strict control of the weight and width of the steel’s coating.
“If you coat more than necessary in the galvanisation process that is an added cost, so it’s important we use as little as possible,” explains Park.
By using AI, POSCO has improved its control of the coating from 84% to 99% in quality deviations.
The data garnered in each individual process contributes to a digital genome for each plate that passes through the plant. The sheer number of data sets POSCO collects has increased exponentially because it samples products every step of the way. This, in turn, is improving quality and increasing customer satisfaction.
“The data allows us to trace back to exactly which operation and at which position a defect in a product occurs,” Park says. “On which shift and on which day, and under what conditions.”
This results in full accountability. It also gives steel producers the opportunity to eradicate defects through continuous closed-loop improvements.
And therein lies the greatest challenge to implementing the smart factory: collecting accurate data. All other processes rely on this vital aspect.
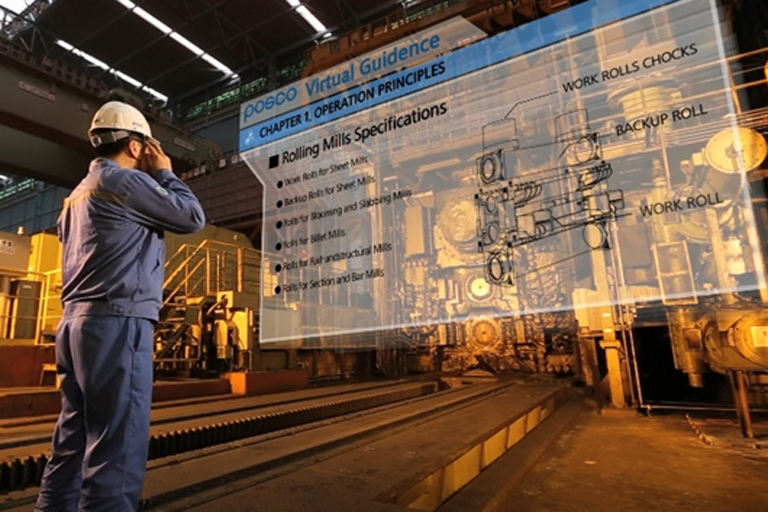
PUTTING THE RIGHT TEAM TOGETHER
Assembling the right team of people is also very tough. A data scientist can come to work at POSCO, but they might not have the specific domain expertise required.
To ensure successful team operations, the company has been running a ‘Smart’ programme to instil its engineers with its ‘Smart culture’ in order to trigger a group-level mind-set change.
Customers and suppliers also have access to the programme, as do young jobseekers.
“Automated processes and plants require employees, who understand how robots function, their requirements, and how they need to be managed.”
Dr Franz Androsch
“Korea’s unemployment is serious at the moment, so we’re also opening up the big data and AI course to them,” Park says.
Despite fears of robots taking jobs from people, the Smart Factory is not leading to a reduction in the operational workforce at POSCO. Instead, an employee is less likely to find themselves on the factory floor and more likely to be analysing data or working in R&D on the next innovation.
For Androsch, these kinds of changes are not surprising. “Automated processes and plants require employees, who understand how robots function, their requirements, and how they need to be managed. That is a lot of work for humans. There are training facilities for employees implemented at the relevant production plants.”
Faced with increasing competition – not just from other steel companies, but a wide range of manufacturers of other materials – steel producers are embracing the opportunities that industry 4.0 presents to increase efficiencies and enhance their sustainability credentials.